Comprehensive Overview: What is Porosity in Welding and Exactly How to stop It
Comprehensive Overview: What is Porosity in Welding and Exactly How to stop It
Blog Article
Porosity in Welding: Identifying Common Issues and Implementing Best Practices for Prevention
Porosity in welding is a prevalent concern that often goes unnoticed until it creates substantial problems with the integrity of welds. In this discussion, we will certainly discover the crucial factors adding to porosity development, examine its harmful impacts on weld efficiency, and talk about the best methods that can be embraced to lessen porosity occurrence in welding processes.
Usual Root Causes Of Porosity

Making use of filthy or wet filler materials can present contaminations into the weld, contributing to porosity issues. To alleviate these typical causes of porosity, extensive cleaning of base metals, correct securing gas selection, and adherence to ideal welding criteria are crucial techniques in achieving top notch, porosity-free welds.
Influence of Porosity on Weld Top Quality

The presence of porosity in welding can significantly jeopardize the architectural stability and mechanical properties of welded joints. Porosity develops spaces within the weld metal, weakening its general stamina and load-bearing ability.
Among the key repercussions of porosity is a decrease in the weld's ductility and sturdiness. Welds with high porosity degrees have a tendency to show lower impact toughness and reduced capacity to deform plastically prior to fracturing. This can be especially worrying in applications where the welded elements go through vibrant or cyclic loading conditions. Porosity can hamper the weld's ability to efficiently send forces, leading to early weld failure and potential safety and security risks in crucial frameworks. What is Porosity.
Ideal Practices for Porosity Avoidance
To improve the architectural honesty and top quality of bonded joints, what specific steps can be carried out to reduce the occurrence of porosity throughout the welding process? Utilizing the proper welding technique for the certain material being bonded, such as readjusting the welding angle and gun placement, can even more avoid porosity. Routine assessment of welds and prompt remediation of any kind of issues recognized during the welding process are essential methods to stop porosity and create top quality welds.
Value of Proper Welding Methods
Applying proper welding techniques is critical in making sure the architectural honesty and high quality of welded joints, constructing upon the foundation of reliable porosity prevention steps. Excessive warmth can lead to boosted porosity due to the entrapment of gases in the weld swimming pool. In addition, making use of the proper welding parameters, such as voltage, current, and travel speed, is crucial for accomplishing audio welds with very little porosity.
Additionally, the choice of welding procedure, whether it be MIG, TIG, or stick welding, must line up with the certain requirements of the task to make sure optimal outcomes. Appropriate cleansing and prep work of the base steel, along with choosing the best filler product, are additionally necessary elements of skillful welding techniques. By sticking to these best techniques, welders can reduce the risk of porosity development and create high-quality, structurally audio welds.
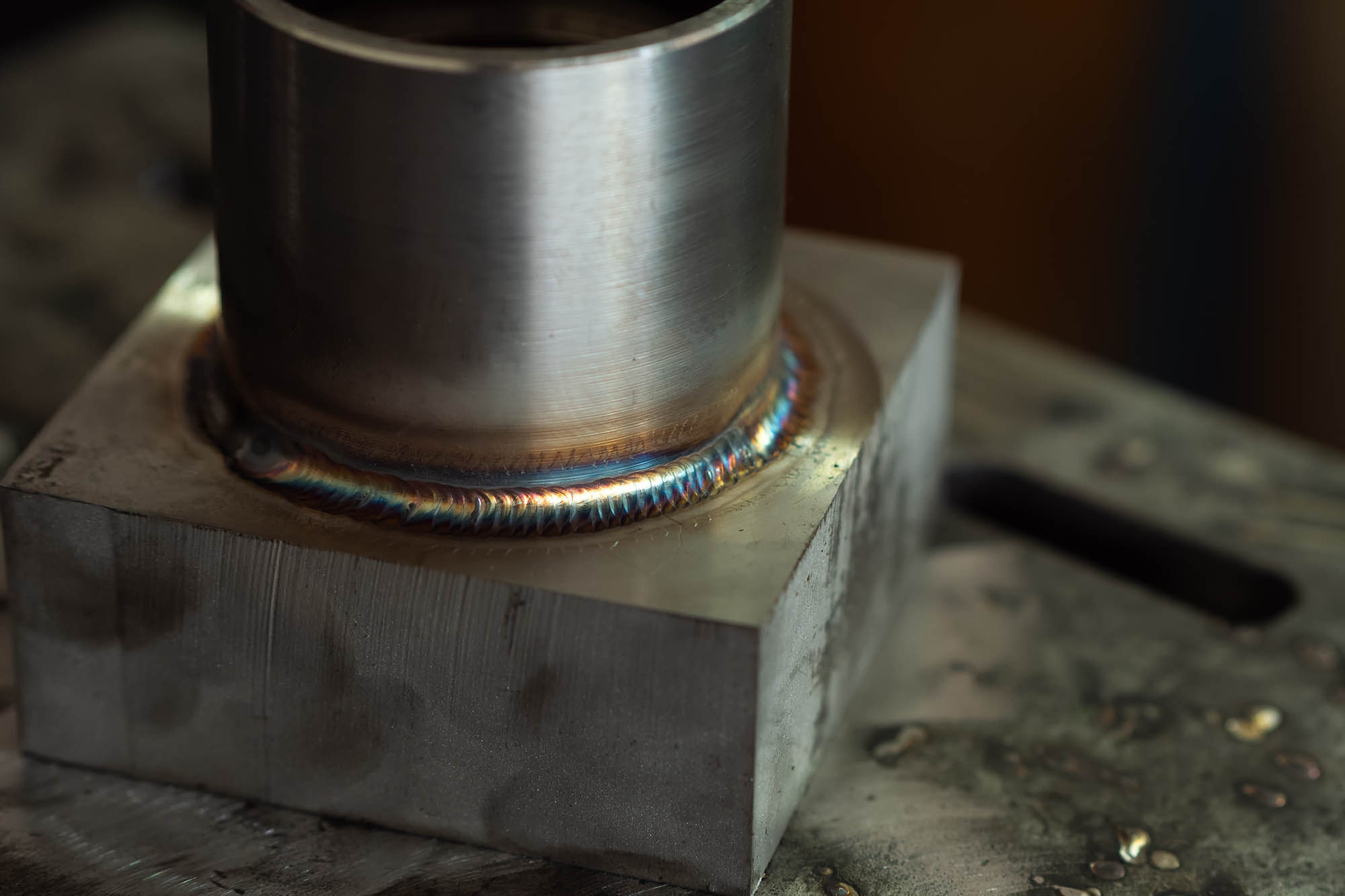
Checking and Quality Control Procedures
Testing treatments are necessary to find and protect against porosity in welding, making sure the strength and sturdiness of the last product. Non-destructive testing approaches such as ultrasonic testing, anchor radiographic screening, and visual evaluation are typically used to recognize potential issues like porosity.
Carrying out pre-weld and post-weld assessments is also essential in maintaining quality control standards. Pre-weld examinations entail verifying the materials, equipment setups, and tidiness of the work area to avoid contamination. Post-weld assessments, on the various other hand, evaluate the final weld for any defects, consisting of porosity, and verify that it satisfies defined requirements. Implementing an extensive high quality control plan that consists of extensive screening treatments and inspections is extremely important to reducing porosity issues visit this site and ensuring the overall top quality of welded joints.
Conclusion
Finally, porosity in welding can be a typical issue that impacts the quality of welds. By recognizing the common sources of porosity and carrying out best methods for prevention, such as correct welding strategies and testing procedures, welders can make sure premium quality and trusted welds. have a peek at these guys It is vital to focus on prevention techniques to reduce the occurrence of porosity and preserve the integrity of welded frameworks.
Report this page